Injection Molding Automotive Parts: A Comprehensive Guide
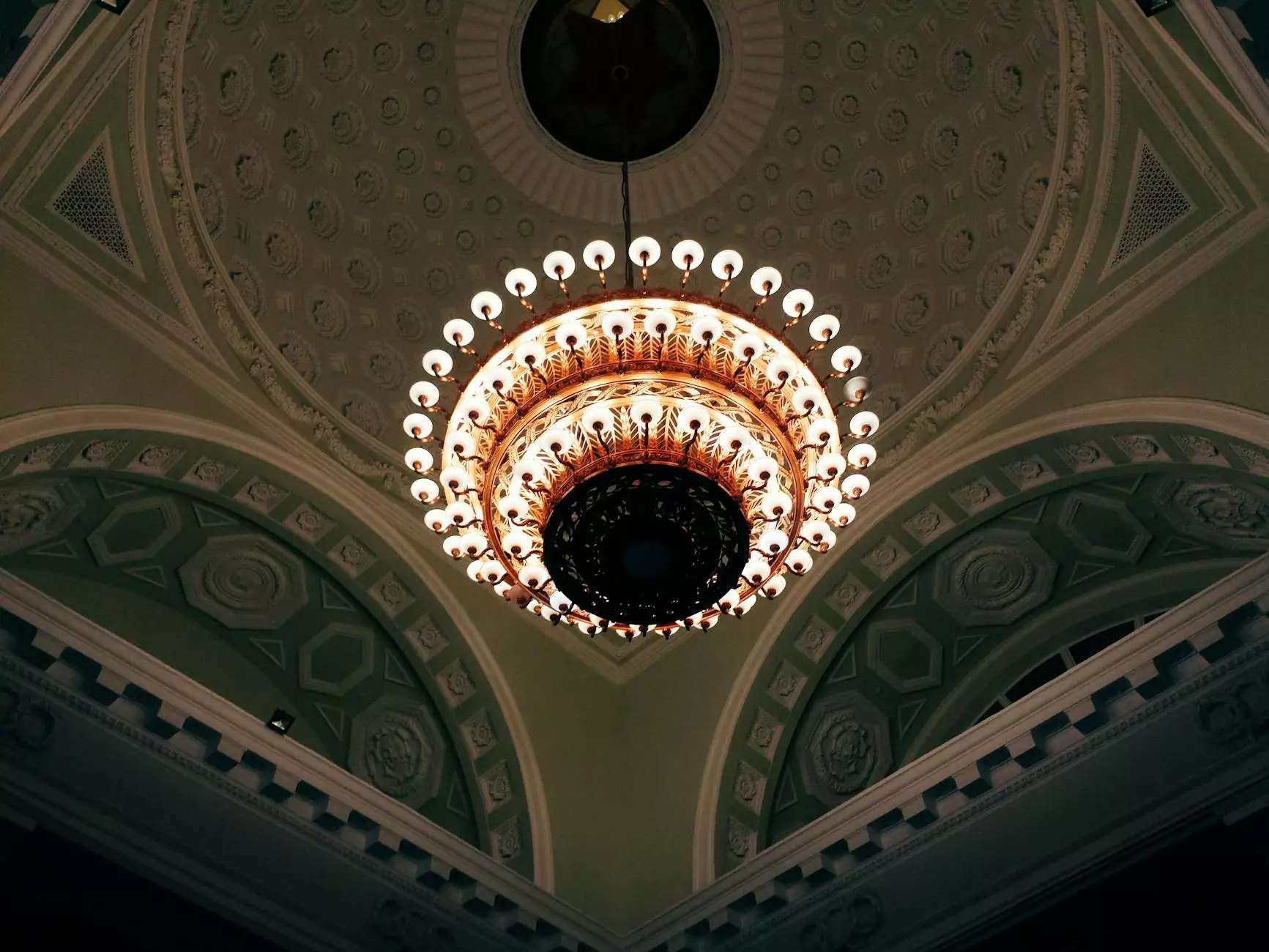
Injection molding has transformed the production of various components across numerous industries. In particular, its application in producing automotive parts has revolutionized the way vehicles are manufactured, making production faster, cost-effective, and more reliable.
Understanding Injection Molding
At its core, injection molding is a manufacturing process where raw material, often thermoplastics, is melted and injected into a mold. Once cooled, the molded plastic solidifies into the desired shape. This efficient method is particularly well-suited for high-volume production runs characteristic of the automotive industry.
Key Benefits of Injection Molding in Automotive Manufacturing
- Cost-Effectiveness: Injection molding reduces waste and lowers production costs significantly compared to traditional manufacturing methods.
- Scalability: It’s ideal for large production volumes, enabling manufacturers to scale up production without compromising quality.
- Precision: The process allows for tight tolerances and complex shapes, ensuring parts fit perfectly.
- Variety of Materials: A wide range of materials can be used, including engineered plastics that offer durability and lightweight properties.
- Reduced Lead Times: With automated systems, injection molding significantly speeds up the production process.
The Process of Injection Molding Automotive Parts
The production of injection molding automotive parts involves several crucial steps, from design to manufacturing.
Step 1: Design and Engineering
The process begins with the design of the automotive part. Engineers utilize Computer-Aided Design (CAD) software to create precise models. During this phase, considerations for mold design, surface finish, and material selection are critical.
Step 2: Mold Fabrication
Once the design is finalized, the next step is the creation of the mold. This stage is essential for determining the quality of the final product. Molds are crafted using high-strength materials to withstand the pressures of the injection process.
Step 3: Injection Process
In this critical phase, raw plastic pellets are fed into the injection molding machine, where they are heated until they become molten. The molten material is then injected into the mold under high pressure and allowed to cool, solidifying into the final part.
Step 4: Cooling and Ejection
Once the part has cooled sufficiently, it can be ejected from the mold. Advanced cooling systems are often employed to expedite this process, increasing efficiency.
Step 5: Finishing Touches
After removal, parts may undergo secondary processes, such as trimming, painting, or assembly, ensuring they meet the final product specifications.
Applications of Injection Molding in the Automotive Industry
The application of injection molding automotive parts can be seen in various components, including:
- Dashboard Components: Intricate shapes and designs can be produced with high precision using injection molding.
- Interior Trim: Lightweight and durable options are favored for aesthetic and functional purposes.
- Exterior Body Panels: Opportunities for customization while achieving a robust structure.
- Functional Components: Parts like clips, housings, and brackets that require high durability.
Challenges in Injection Molding of Automotive Parts
Despite its advantages, the injection molding process does come with challenges that manufacturers must address:
- Initial Setup Costs: The cost of designing and fabricating molds can be substantial, but is often offset by lower production costs over time.
- Material Limitations: While numerous materials can be molded, specific requirements may limit choices based on temperature tolerance and other factors.
- Complexity of Parts: Certain designs may result in issues like warping or sink marks, necessitating careful design and engineering.
Future Trends in Injection Molding in the Automotive Sector
The future of injection molding automotive parts looks promising, with several trends shaping the industry:
1. Sustainability and Eco-friendly Materials
With growing environmental concerns, manufacturers are increasingly focusing on using recyclable materials and developing bioplastics. This transition not only addresses environmental issues but also enhances brand loyalty among eco-conscious consumers.
2. Advanced Technologies
Integrating technologies such as 3D printing and AI can streamline the design and manufacturing processes, leading to rapid prototyping and production efficiency. Additionally, smart monitoring systems are improving quality assurance throughout the supply chain.
3. Customization and Personalization
As consumers seek more personalized vehicles, the ability to customize components through injection molding becomes increasingly desirable. Manufacturers who can accommodate these requests will likely gain a competitive edge.
DeepMould.net: Your Partner in Injection Molding Automotive Parts
At DeepMould.net, we specialize in delivering high-quality injection molding automotive parts that meet industry standards. Our experienced team harnesses innovative techniques to ensure our products are efficient, reliable, and tailored to our clients' needs.
Conclusion
In conclusion, injection molding is a vital aspect of modern automotive manufacturing. Its ability to produce high-quality, precise, and varied components at scale allows automotive manufacturers to innovate continuously. By embracing advancements and meeting consumer demands, businesses like DeepMould.net play a pivotal role in shaping the future of automotive production.
Experience the benefits of injection molding for your automotive parts by partnering with us for your manufacturing needs. Contact DeepMould.net today!