The Future of Business in Mold Injection Plastic
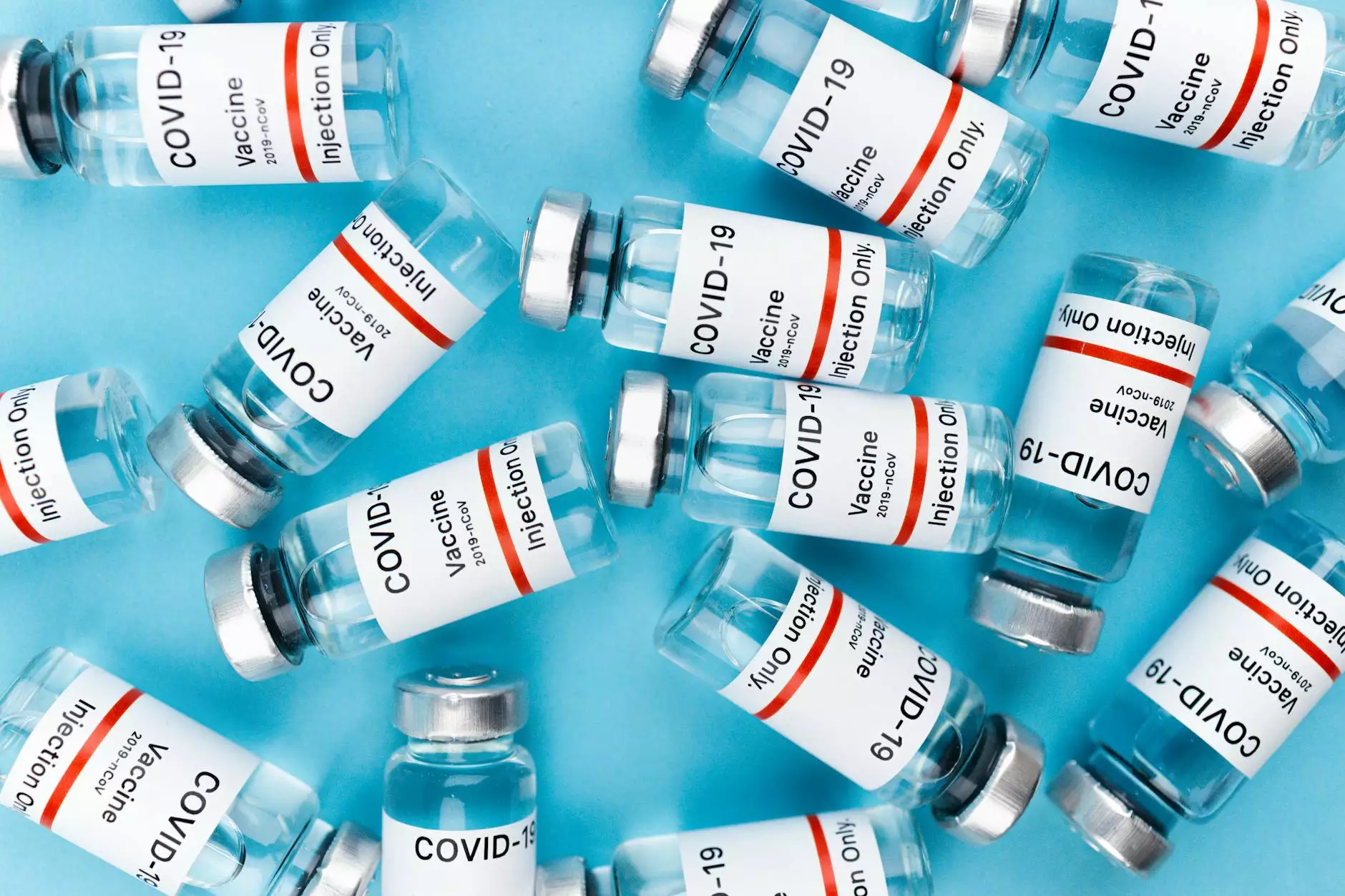
Mold injection plastic has become a cornerstone of modern manufacturing and design, offering unparalleled advantages in efficiency, versatility, and scalability. Businesses that leverage the power of this technology are well-positioned to thrive in today's dynamic marketplace. In this comprehensive article, we will explore the various facets of the mold injection plastic industry, including its significance, applications, and future trends.
Understanding Mold Injection Plastic
Mold injection plastic is a manufacturing process used to produce plastic parts by injecting molten plastic into a mold. The process involves several key stages:
- Material Selection: Different types of plastics can be used depending on the desired properties of the final product.
- Mold Design: Precision is key in mold design, where the specifics of the part being produced must be accurately reflected.
- Injection Process: Molten plastic is injected into the mold at high pressure, filling the cavity.
- Cooling: The molten plastic is allowed to cool and solidify within the mold.
- Demolding: The finished part is then removed from the mold, ready for further processing or assembly.
The Significance of Mold Injection Plastic in Business
The impact of mold injection plastic on business operations cannot be overstated. Here are several reasons why it plays a critical role:
1. Cost Efficiency
One of the primary advantages of mold injection plastic is its ability to produce parts in high volumes with minimal waste. The efficiency of the process means that businesses can achieve significant cost savings. By utilizing advanced materials, companies can enhance the durability and functionality of their products while keeping production costs low.
2. High Precision and Consistency
The precision achieved through mold injection means that products can be made to exact specifications. This is particularly important in industries such as automotive and medical devices, where tight tolerances are essential. Consistency in manufacturing ensures that each product performs identically, crucial for maintaining quality standards.
3. Versatility in Design
Mold injection plastic allows for a wide range of designs, from simple shapes to complex geometries. The flexibility in design opens up possibilities for innovation, enabling businesses to develop products that meet specific consumer needs. This capability encourages businesses to adopt a customer-centric approach, tailoring products to satisfy diverse market demands.
4. Rapid Prototyping
The mold injection process facilitates rapid prototyping, allowing businesses to produce prototypes quickly and efficiently. This speeds up the development cycle, enabling companies to test and refine their products before full-scale production. The ability to iterate quickly is a significant advantage in today’s fast-paced business environment.
Applications of Mold Injection Plastic
The applications of mold injection plastic are diverse, spanning across multiple industries, including:
1. Automotive Industry
The automotive sector relies heavily on mold injection plastic to produce various components such as dashboards, interior panels, and exterior trim. The lightweight and durability of plastic parts contribute to fuel efficiency without compromising safety.
2. Consumer Goods
From packaging to household items, mold injection is utilized extensively in the consumer goods market. Its ability to produce intricate designs at a low cost makes it ideal for products ranging from toys to kitchenware.
3. Electronics
In the electronics industry, mold injection plastic is key in creating casings and components for devices such as smartphones, computers, and appliances. The use of plastics helps in reducing weight and improving aesthetic quality.
4. Medical Devices
The production of medical devices involves stringent regulatory compliance, and mold injection plastic offers the precision and reliability required in this field. Components such as syringes, surgical tools, and drug delivery devices are often produced using this method.
Trends Shaping the Future of Mold Injection Plastic
The mold injection plastic industry is constantly evolving. Here are some key trends expected to shape its future:
1. Sustainable Practices
With increasing environmental concerns, businesses are seeking sustainable alternatives in their production processes. The adoption of bio-based and recyclable plastics is rising, with companies looking to reduce their carbon footprints. Innovations in eco-friendly materials will play a significant role in the coming years.
2. Automation and Industry 4.0
The integration of smart technologies and automation in manufacturing is revolutionizing the mold injection process. Advanced robotics and AI enable greater efficiency, improved quality control, and reduced human error. Businesses that embrace Industry 4.0 technologies will likely gain a competitive edge.
3. Customization and Personalization
Consumers are increasingly demanding personalized products. Advances in mold injection technology allow for customized production runs, enabling companies to cater to niche markets while avoiding bulk production costs. This trend is leading to more sustainable manufacturing practices as well.
4. Digital Twin Technology
Digital twin technology enables businesses to create virtual replicas of their production processes. This allows for real-time monitoring and optimization of mold injection operations, leading to increased efficiency and reduced downtime.
DeepMould.net: Innovating in Mold Injection Plastic
As a leader in the mold injection plastic sector, DeepMould.net is committed to delivering high-quality products and services to meet the evolving demands of the industry. With a focus on innovation, DeepMould.net utilizes cutting-edge technologies and materials, ensuring excellence in every project.
Why Choose DeepMould.net?
Here are a few reasons why DeepMould.net stands out in the competitive landscape:
- Expertise: With years of experience in mold injection plastic, the team possesses deep knowledge of materials and processes.
- Advanced Technology: Utilization of the latest machinery and software for optimal design and production efficiency.
- Customer Focus: A commitment to understanding client needs and delivering tailored solutions that exceed expectations.
- Quality Assurance: Rigorous testing and quality control measures to ensure every product meets industry standards.
Conclusion
The landscape of business in mold injection plastic is rich with opportunities as companies adapt to changes in technology, consumer preferences, and environmental concerns. Understanding the nuances of this robust market is essential for success. By partnering with experienced organizations like DeepMould.net, businesses can ensure they remain at the forefront of innovation and efficiency in product development.
Through a commitment to quality, sustainability, and customer satisfaction, the future of mold injection plastic is bright. Embrace this technology today to unlock new possibilities for your business.
© 2023 DeepMould.net. All rights reserved.