The Importance of CNC Turning in Modern Manufacturing
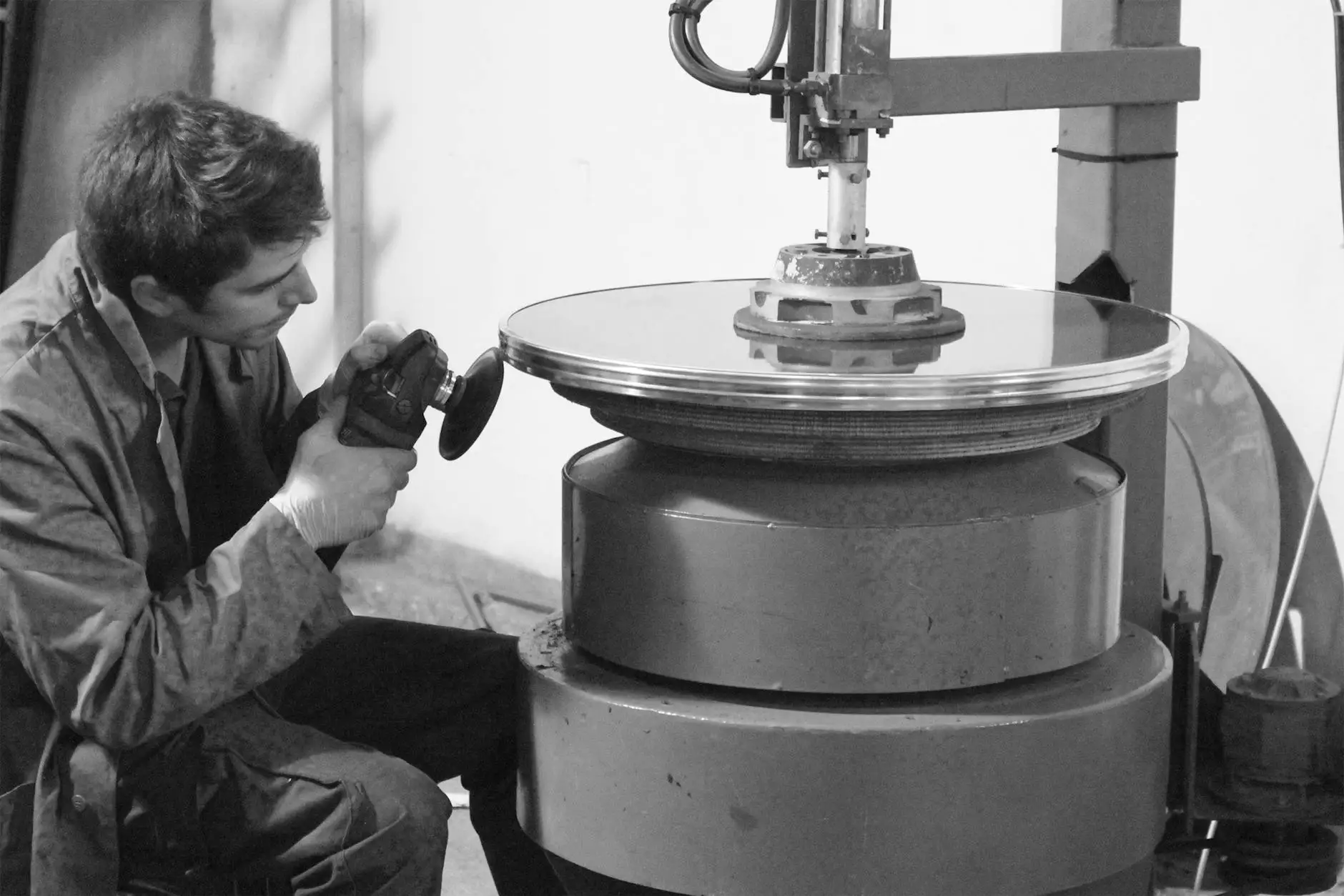
The advancement of technology has reshaped the landscape of manufacturing, with CNC (Computer Numerical Control) machining leading the way. Among the various CNC processes, turning stands out as a critical method, especially for creating precise and intricate parts. A pivotal player in this arena is the China CNC turning parts manufacturer, which has increasingly become integral to global supply chains.
What is CNC Turning?
CNC turning is a precise machining process that involves rotating a workpiece against a cutting tool to create cylindrical parts. This method is widely used for producing components with a wide range of diameters and lengths. The manufacturing capabilities of a CNC turning process can deliver high-accuracy results, ensuring that parts meet stringent specifications and tolerances.
Why Choose a China CNC Turning Parts Manufacturer?
China’s manufacturing industry has witnessed tremendous growth, largely due to its focus on innovation, technology adoption, and skilled labor. The decision to partner with a China CNC turning parts manufacturer offers several advantages:
- Cost Efficiency: Manufacturers in China often operate at lower production costs, resulting in significant savings for businesses looking to outsource.
- Access to Advanced Technology: Many Chinese manufacturers leverage cutting-edge machinery and CNC technology, ensuring better precision and efficiency in production.
- Scalability: Chinese manufacturers have the infrastructure to handle large-scale production and are capable of rapid turnaround times.
- Diverse Material Options: A variety of materials, including metals and plastics, can be machined, providing flexibility for different projects.
Key Factors to Consider When Choosing a CNC Manufacturer
When selecting a China CNC turning parts manufacturer, it’s essential to evaluate several critical factors:
- Experience and Reputation: Look for manufacturers with a proven track record and positive reviews from previous clients.
- Quality Assurance: Ensure the manufacturer has stringent quality control measures in place, including certifications such as ISO 9001.
- Technical Capabilities: Assess the range of machinery and technology the manufacturer utilizes and whether they can handle your specific requirements.
- Communication: Choose a manufacturer that demonstrates excellent communication, including providing updates throughout the production process.
The CNC Turning Process: A Step-by-Step Overview
The CNC turning process involves several stages:
1. Design and Programming
The journey begins with the design of the part using Computer-Aided Design (CAD) software, which is then translated into a CNC program. This program contains all the necessary instructions for the machine to follow, ensuring precision and replication of the intended design.
2. Material Preparation
The selected material is prepared according to specifications, including ensuring appropriate dimensions and surface conditions for effective machining.
3. Machining Process
During this phase, the CNC lathe machine rotates the workpiece while a fixed cutting tool removes material to achieve the desired shape and finish. This high-speed operation produces parts with excellent surface finishes and tight tolerances.
4. Quality Control
After machining, parts undergo rigorous quality inspections to ensure they meet all specifications. This can include dimensional checks, surface roughness measurements, and functional testing.
5. Finishing Touches
Finally, any necessary finishing processes such as polishing, anodizing, or coating are applied to enhance the part’s performance characteristics and aesthetic appeal.
The Role of Quality Assurance in CNC Turning
Quality assurance is paramount in CNC turning. A reputable China CNC turning parts manufacturer implements comprehensive quality control measures at every stage of the production process. This ensures that the final products not only meet but exceed customer expectations. Key quality assurance practices include:
- Regular Equipment Calibration: Ensuring machines are calibrated to maintain precision.
- Non-Destructive Testing: Techniques such as ultrasonic or magnetic particle inspection to ensure part integrity.
- Documentation and Traceability: Keeping detailed records of materials, processes, and inspections for future reference.
Innovations in CNC Turning Technology
The manufacturing sector continually evolves, and CNC turning is no exception. Recent innovations have enhanced the capabilities and efficiency of CNC turning processes:
- Multi-Axis Machines: These machines can operate on multiple planes, achieving complex geometries without the need for multiple setups.
- Adaptive Control Systems: These systems can adjust machining parameters in real time based on feedback, improving the efficiency and quality of production.
- Automation and Robotics: Increased automation in CNC turning reduces manual labor, speeds up production, and minimizes the risk of errors.
Conclusion: The Future of CNC Turning in Global Manufacturing
As industries strive for greater efficiency and precision, the role of the China CNC turning parts manufacturer will continue to grow. By leveraging advanced technology, skilled labor, and a commitment to quality, these manufacturers are setting new standards in parts production.
In conclusion, whether you're in the automotive, aerospace, or electronics sector, partnering with a reliable CNC turning manufacturer in China can significantly enhance your production capabilities. With numerous advantages, including cost savings, advanced technology, and a wide range of materials, these manufacturers are essential in meeting the demands of modern industries.
For businesses seeking to thrive in today's competitive landscape, collaborating with a premier manufacturer like Deep Mould at deepmould.net could be the key to unlocking unparalleled precision and quality in CNC turning parts. As the industry continues to innovate and adapt, the future holds exciting possibilities for both manufacturers and their partners.